

EVAPORATION TECHNOLOGY

The evaporators designed by L & M Engineering are unique and different from the usual ones because they operate under the principle of "Descending Turbulent Mist (NTD)", which consists of thermally “exploding” the incoming liquid through a partial flash, resulting in a mixture of vapor and small liquid particles (mist).
This mist is generated in each of the distribution cones which feeds the tubes of each stage of the evaporator.
Unlike the falling film technology, turbulent descending mist does not relies on mechanical devices for the distribution of liquid in the tubes. The use of mechanical devices often result in uneven distribution, which leads to localized heating and, consequently, to the burning of the product in the walls of the tubes. In the evaporator designed by L & M, the mist is evenly distributed due to the pressure equilibrium inside the tubes. In this way, when the flow in one tube increases, the pressure inside it increases and the product automatically distributes to another tube.
The mist product falls freely through the open tubes, absorbing the heat and evaporating the water, further increasing its volume. It is then thermally accelerated reaching very high speeds (in some applications, near the sonic speed) at the end of the tubes.
The configuration of an evaporator varies a lot depending on the product characteristics the desired energy consumption, the vacuum system, etc. Several factor can be changed to achieve the best configuration such as distribution of the heat exchange surface, the lengths and diameters of the tubes, the speed control of the product, the number of effects, the arrangement of the preheaters, etc.


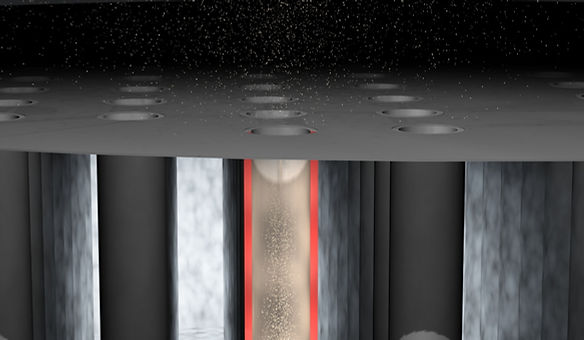
• Longer operation time between cleanings.
Due to the high speed of the product, its uniform distribution and the absence of localized heat, the incidence of incrustations inside the tubes is drastically reduced.
This differential causes the period of operation between the cleanings to be prolonged substantially.
Depending on the product to be concentrated, the evaporator can operate for up to several days without the need to be cleaned.
• Low maintenance cost.
In our evaporator, the only movable parts are the pumps and the motors. Therefore, maintenance is usually restricted to the replacement of mechanical seals, bearings and couplings.

RESEARCH AND DEVELOPMENT (R & D)
Aiming at researching and developing of new products or even the possibility of a new process for an already developed product, L & M Engenharia Ltda has designed, built and makes available to its current and future customers a Pilot Evaporator.
It is an industrial evaporator of small proportions, easy to be transported and installed and that presents the same efficiency and advantages of our evaporators (ECoFluid - fluid concentration evaporator) of great dimensions and capacities.
The use of our pilot evaporator as well as the operational tests in an industrial unit allow the evaluation and determination of its performance and the quality of the concentrated product.
The principle of N.T.D gives our evaporators significant advantages, such as:
• Less time of exposure to heat.
Our evaporators are single step, non-recirculating, with multiple effects and stages. Due to the high speed of the product, heat transfer to it is done quickly.
In this way, the exposure time of the product to the heat is considerably smaller increasing the product quality and reducing the possibility of localized heating.
• No localized heating.
The principle of operation of our evaporators (N.T.D.) does not require mechanical devices for product distribuition. It also facilitates the uniform distribution of the product inside the tubes by means of pressure equalization. Uniform distribution prevents localized heating and consequent burning of the product.
• Simplicity of operation.
Variations in evaporation capacity and degree of concentration are obtained by simple regulation of the steam and product flows.
• CIP - Clean in Place System.
The cleaning procedure is very simple and can be carried out by the same operator who should only open and close some valves, without changing the operating conditions. That is, there is no need to disassemble any parts of the evaporator at the time of cleaning.
Because of its simplicity, this system can be easily automated.